|
<11. 三つの保全 その2「印刷品質保全」安定品質の為に>
次に、フォームを固めなければいけない。機械はばっちりだということで球はどんどん投げる。ところが全然ストライクが入らない。こういうことでは話になりませんので、フォームを固めなければならない。これが「印刷品質保全」というふうに私が名付けたものです。
印刷は複合技術です。ですから、品質を総合的に管理していく保全が必要です。
「印刷の七つ道具」という言葉がありますが、ご存じでしょうか。三つでも四つでも分類は別に構いません。分類の仕方がいろいろあるということです。私は、語呂がいいので一度聞いたら忘れられなくて済むということで「七つ道具」という言葉を使わせていただいております。
|
|
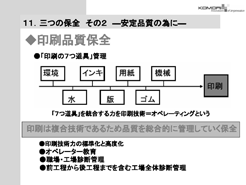 |
画像をクリックして拡大(PDF) |
|
環境、水、インキ、版、用紙、ゴム、機械、この七つを統合するのを印刷技術、オペレーティングといって、それによって印刷をする。
この七つ道具を管理していくことが必要だと思います。たとえば、印刷環境が、朝は10度である、お昼になったら25度ある、夕方になったら40度ある、これではフォームは変わってしまいます。当然インキはドロドロになります。朝と昼と夜では印刷の網点が違う。それで同じものを刷れといっても無理な話です。ですから、環境や水やインキなどをすべて同じように投げられるようにコントロールする、管理していくということが必要になると思います。
そのためには、そういう七つ道具だけではなくて、印刷技術力というものも管理しなければなりません。教育ということも必要でしょう。バブル景気の中の「回せ、回せ」一辺倒の産物ともいえる現場オペレータの「私使う人」「私スイッチを押す人」、つまりスイッチマン化まですすんでいると業界全体で言われています。スイッチマンではフォームが変わってしまいます。ボタンを押すしかできません。
更に、工場や全体の診断ということも必要だと思います。プリプレスからポストプレスまで、全体を管理する。そのような総合的な管理、これが「印刷品質保全」です。
その内容全部をご紹介することはできませんので、一部分だけご紹介したいと思います。
|
|
|
|
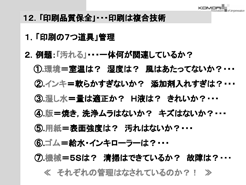 |
画像をクリックして拡大(PDF) |
|
 |

<12.「印刷の7つ道具」……印刷は複合技術>
まず七つ道具。たとえば「汚れる」というような現象があったとき、「小森さん、印刷物が汚れるので来て下さい」と電話がかかってきます。跳んでいきますと、印刷機械の給水装置のレバーにガタがあった、あるいはエアシリンダーが壊れていたとかということで、当然それは汚れます。機械が悪いわけですから。
でも、機械故障は10%もないのです。サービスマンは何をしているか。ローラーはどうなっているんだろうか、ローラーを調整してみよう、交換してみよう、水はどうかな、ドロドロだ、交換しよう。インキもドロドロ、こんなことをやらせていただいているわけです。
つまり、環境によっても汚れます。インキによっても汚れます。あるいは湿 |
し水、版、用紙、ゴムによっても汚れます。これら七つを管理しないかぎり、この汚れから解放されることはないのです。これは、一つの例です。 |
|
|
|
<13. 環境・資材管理>
非常に重要な環境管理あるいは資材管理というものをお話ししたいと思います。工場の温湿度が許容値に入っていないと色が変わってしまうというお話をさせていただきます。 こちらに、「オフセット枚葉印刷Japan Color オペレーションガイド」というのがあります。ジャパンカラー2001は枚葉機の日本の色を決めたわけです。そもそも日本の白とは何か。日本の黒とは何か。日本の赤とは何か、ということを決めたわけです。これを「ジャパンカラー」と名付けました。 この色を出すためにはこういう環境でないと出ませんというのが書いてあります。この条件が整わない限りこの日本の色は出ないということです。
工場内の温度なら25±3℃、工場の湿温なら55±5%、こういうものでないと、これは赤といっても赤ではないといっているわけです。 |
|
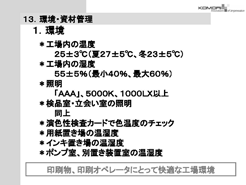 |
画像をクリックして拡大(PDF) |
|
|
|
|
あるいは照明でもそうです。皆さま演色性検査カードというものをご存じでしょうか。これは、アイグラフィックス社が作っているものです。
二つの色があります。いま二つの色は別々の色になっております。今このホールの照明の色温度は、5,000K(ケルビン)ではないということです。5,000Kというのは太陽の昼間の光です。その下で見ると、この二つは同じに見えるのです。光には色温度というものがあるのです。光によって色は変わって見えるのです。
ですから、3,000Kくらいの電球色の場合は赤っぽく見えます。昼白色が5,000K、それから一般的な蛍光灯などの昼光色は7,000 Kぐらいですから、白っぽく、青っぽく見えます。夜のマンションなどを見ると、赤い光と白っぽい光があると思います。その下で見えるものは色が違ってみえるわけです。こういう照明を管理しなかったら日本の色は出ませんということです。ほとんどのオペレータスタンドは、特殊な昼白色の蛍光灯を使っています。
ところが、ときどき見かけるのは、オペレータスタンドの脇にテーブルが置いてありますが、そこの上の蛍光灯は普通のものです。そうしますと青っぽく見えるはずです。そこで色を見て、「青っぽいな」とかいっている人がいます。あるいは、応接室や検品室にクライアントのデザイナーが来て、「色はどうですか」、デザイナーが来て「ちょっと赤っぽいな」「青っぽいな」という。
その蛍光灯が太陽光ではない。普通の蛍光灯を使っている。そうすると青っぽく見えます。クライアントは、「俺のイメージはもっと赤いんだ。もっと赤くしてくれ」という。オペレータは一生懸命赤くする。「OK」となる。店頭に出たら真っ赤。「何だ、これは」という話になってしまいます。つまり、色の問題というものは光によっても変わるということです。
ですから、印刷物、あるいは印刷オペレータにとって快適な工場環境というものを作っていかないと、色を管理することはできないということだと思います。 |
|
|
|
|
|
<資材>
資材管理も必要です。1〜4・・・号機、全部使っているものが違う。ブランケットは違う、インキは違う、仕立ても違う、ローラーも違う、全部違う。これで同じものを投げろといったって、それは投げようがないです。
Aさんの資材、Bさんの資材、Cさんの資材、全部違う。これで同じものを投げろ、安定させろ、品質を安定させろというと、どうなるか。その人の個人技になる。Aさんは上手投げ、Bさんは横投げ、Cさんは下手投げというように。ですから、資材も全部絞り込んで、選択する。そしてその使用方法を標準化する。こうしなければフォームは崩れてしまうと思います。 |
|
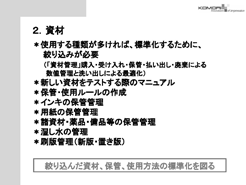 |
画像をクリックして拡大(PDF) |
|
|
|
|
<14.「印刷機械の標準化」のためのポイント>
ポイントは胴仕立て、それからインキローラーなどのゴム関係です。ゴム関係は非常に印刷物に影響を与えますので意識的にぜひ管理していただきたいと思います。あるお客様で8色機が入っておりまして、全然色が合わない。見当が合わない。いろいろ調べ、そうしたら、私びっくりいたしましたが8色のうちの4色のブランケットが違う。どうしてかと聞いたら、「メーカーが新しくこんなのをつくったから、試しに使ってくれ」という。
4色分だけ変えるのではなく、8色全部変えてくださいよ。これで合うわけありません。私はスイッチマンだなと思いました。
それではやはり同じものは投げられないと思います。ですからブランケット、あるいは胴仕立てについては精密機械として厳密な管理が必要です。 |
|
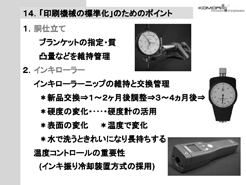 |
画像をクリックして拡大(PDF) |
|
「下紙何枚入ってますか」「わかんない」とか、「いや、たしかこんな感じだよ」では困るのです。
それからインキローラー。ゴムローラーですので当然伸縮します。ニップは変わります。ニップを管理しなければ当然転移性が変わる、転移性が変わるからどうするか。大量に壺を開いていっぱいインキを出す。ドットゲインが変わる。濃度が変わる。その時はうまく刷れてOKだった、しばらくしたらドライダウンで全然色が変わってしまったということにもなるのです。ですから、ローラーの管理もしていただかなければならないと思います。そのためには、測定器を使って管理するということも必要だろうと思います。
給水ローラーもそうです。この給水ローラー、湿し水、この管理はとても大事だと私は思います。昔からいわれておりますが、「水を制するものは印刷
|
|
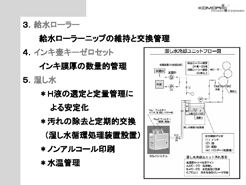 |
画像をクリックして拡大(PDF) |
|
|
|
|
を制す」、これはいまも真理だと思います。
私がいろいろなところでお話をさせてもらって、現場を指導させていただいて、水関係を見せて頂きます。やっぱりここの印刷会社のオペレータは一流だなと思ったそういう会社の機械の水を見たら、必ずきれいです。必ずきれいだから一流かどうかというのは、逆は真ならずですが、一流といわれているところの水は必ずきれいです。そして給水ローラーニップを見たら必ず決まっています。そうでなければ品質を維持できないのです。ですから、意識的にぜひ管理していただきたいと思います。
いままでがフォームを固めるというお話でした。 |
|
|
|
|
|
次へ→ |
|